American Plastic Molds are used in the production of a large variety of products and tools. From the base of a machine screw to the shell of a household appliance, they play a crucial role in our daily hardware and industrial production.
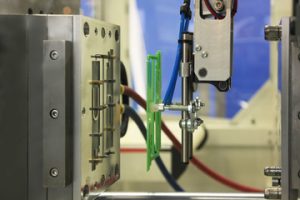
However, plastic molding is a long and complicated process, so it’s important to avoid common mistakes that can set you back weeks or thousands of dollars.
The process of creating plastic molds requires a lot of preparation and time. First, you need to select the material that is appropriate for your product. You must also ensure that the design is accurate to avoid errors in the final product. Once the plastic is molded, you must remove it carefully to prevent damage to the item. The process can take 16 weeks to complete. It is best to choose a company that offers a quick turnaround time.
The injection molding process uses high temperatures and pressure to make a product from liquid plastic. This method is best suited for producing small parts with tight tolerances and complex shapes. It is also used for larger parts such as car components. The injection molding process is not easy to master, but it can be very efficient when done correctly. The key to success is using the right tools and techniques.
Vacuum forming is a low-pressure method of making plastic products. This method does not require the molding to be heated to a molten state, which means that the mold can be made from cheaper materials. It is also easier to operate, as the pressure and precision requirements are lower than in injection molding. It is important to use high-quality, corrosion-resistant materials, such as pre-hardened steel or low-carbon martensitic aging steel, which have better cutting, heat treatment and polishing properties.
Injection molds are used for a wide range of applications, including consumer products and automobile parts. This method is the most popular in the world, and it can be used to create a variety of shapes and sizes. It is a cost-effective way to produce large volumes of parts, and it is suitable for most types of plastics. The plastic can be made into a wide variety of shapes and sizes, and it is very durable.
Blow molding is a process that uses low pressure to make plastic products. The plastic is poured into a closed, hollow mold and then rotated. This causes centrifugal force to coat the walls of the mold evenly. The excess plastic is then drained from the mold. This method is best suited for large, hollow parts, such as storage tanks and road cones. This technique produces a very strong, lightweight product and can be used as a replacement for metal parts.
Types
Plastic is an integral part of daily life, and it can be molded into a variety of shapes. Its use is rapidly increasing, and it can even replace multiple traditional metal parts. This is due to the fact that a reasonably designed plastic part can be much cheaper and easier to produce than a similar metal one.
Plastic molds are special tools that give plastic products their final shape and precise size. They are used in various types of injection molding processes and can be made of different materials. In general, they are mainly composed of a pouring system and a temperature regulating system. The latter is the most important component, because it is in direct contact with the liquid plastic and changes with it. In addition, there are many other parts in the mold that affect its structure and processing quality.
Depending on the type of plastic product, there are several different kinds of plastic molds. These include injection molds, blow molds, and rotational molds. The injection molds are the most common, and they have a variety of features that make them perfect for producing large quantities of high-quality plastic products. Injection molds are available in a range of sizes, and they can be produced with or without inserts. Injection molds can also be cooled by air or water. Water-cooled molds are more efficient than air-cooled ones, but they may be slower to cool.
In addition to injection molds, blow molds are a popular method of plastic production. This process uses a hollow cavity to form the desired plastic product, and it can be used for both thermoplastic and elastomeric materials. Injection molds can also be shaped to produce blow-molded plastics, but this is usually not a viable option for larger products.
Rotational molds are used for making a variety of complex-shaped plastic products. This process involves rotating the raw material around a core to create the desired shape, and it is more cost-effective than other types of plastic molding. Rotational molds can be made of metal, plastic, or a combination of both, and they can include logos and other details for finished products.
Pricing
Plastic molds can be a costly investment, especially for high volume production runs. But there are ways to keep costs down while getting the results you need. By carefully considering the size and complexity of your project, you can find a cost-effective solution for your next batch of plastic parts.
The first thing to consider is the type of plastic resin you will use for your injection molding project. Some materials require more processing energy than others, so you may need to pay extra for this. Also, be sure to choose a plastic resin that is safe for the environment and your customers.
Another factor that affects price is the amount of time the plastic mold needs to produce a single part. The lower the cycle time, the lower your per-part cost will be. Likewise, the number of identical cavities in your injection mold can also affect your cost per part rate.
Injection molding is a versatile process that can be used to create a variety of different plastic products. It can be used to make anything from small embryonic head screws and buttons to large industrial containers and car parts. There are a number of different methods for plastic molding, but three stand out as the most popular: injection molding, insert molding, and rotational molding.
Injection molding uses a high-pressure injector to force liquid plastic into a cavity. The resulting solid product is then cut off from the rest of the plastic by a cutting tool. This method is ideal for producing large, uniform parts that will be sold in bulk.
Insert molding is a more advanced process that involves combining pre-fabricated metal inserts with injection molded plastic to create a single, integral component. This technique is commonly used to manufacture the various components of remote controls, such as buttons, battery cover, and casing.
The type of plastic molding materials you use will also impact your final cost. For example, steel is more expensive than aluminum but can last longer and be easily modified for design changes. Aluminum, on the other hand, cannot be modified and is prone to wear and tear over time, which will increase your overall cost.
Time
The time it takes to create a plastic mold is a key factor in determining the feasibility of plastic molding projects. Evaluating mold complexity helps manufacturers identify areas for improvement and optimize manufacturing processes to meet production goals within budget. Various plastic molding techniques exist, each with its own unique advantages and limitations. Understanding these options helps manufacturers select the best one for their project needs and strategic objectives.
The fabrication time for a plastic mold is directly related to the complexity of the design and the desired output quality. Prototype molds, which are used for initial testing and validation of a design, take less time to make since they don’t require the same level of durability as production molds. On the other hand, production molds take significantly longer to fabricate because they must be made from a harder material to ensure their longevity.
Injection and cooling times also influence the overall plastic molding process. Injection times are influenced by the amount of pressure applied, the power and temperature of the injection machine, and the plastic’s melting point. Cooling times are influenced by the size and shape of the plastic part, which impacts how much heat is transferred to the interior mold. Using efficient cooling channels and choosing plastics with favorable flow characteristics can help speed up the process.
Other determinants of plastic molding costs include material and shipping expenses. The cost of raw materials can fluctuate based on supply chain conditions and market conditions, while transportation expenses are impacted by the distance and weight of the product. The use of a comprehensive plastic molding price estimator helps manufacturers understand and control these variables to avoid costly overages.
Determining the number of units to be produced is another important determinant of plastic molding costs. Accurate demand forecasting supports streamlined production scheduling that balances efficiency with resource optimization. The Phasio platform’s cost estimation tools streamline this process, enabling manufacturers to estimate costs quickly and confidently.